High Frequency Welded Pipes Technology, Applications, and Importance
High frequency welded pipes, often abbreviated as HFW pipes, represent a significant advancement in the field of pipe manufacturing. These pipes are fabricated through a process that involves welding steel strips or sheets using high-frequency electrical currents. The technology behind this method is based on the principle of eddy current heating, which generates heat at the contact point of the metal surfaces, facilitating a strong and seamless weld.
The process begins with the feeding of cold-rolled steel coils into a forming machine, which shapes the strip into a cylindrical form. The edges of the strip are then brought into contact and subjected to an alternating high-frequency electric current. This current produces heat due to resistive losses, causing the edges to melt and fuse together, creating a continuous weld. The pipe is then cooled, straightened, and cut to the desired length, resulting in a high-quality, uniform pipe.
One of the key advantages of high frequency welded pipes lies in their superior strength and durability. The welding process ensures a consistent and defect-free joint, making them suitable for various applications where high pressure and mechanical stress are involved. Additionally, HFW pipes have a smooth internal and external surface, reducing flow resistance and enhancing efficiency in fluid transportation Additionally, HFW pipes have a smooth internal and external surface, reducing flow resistance and enhancing efficiency in fluid transportation
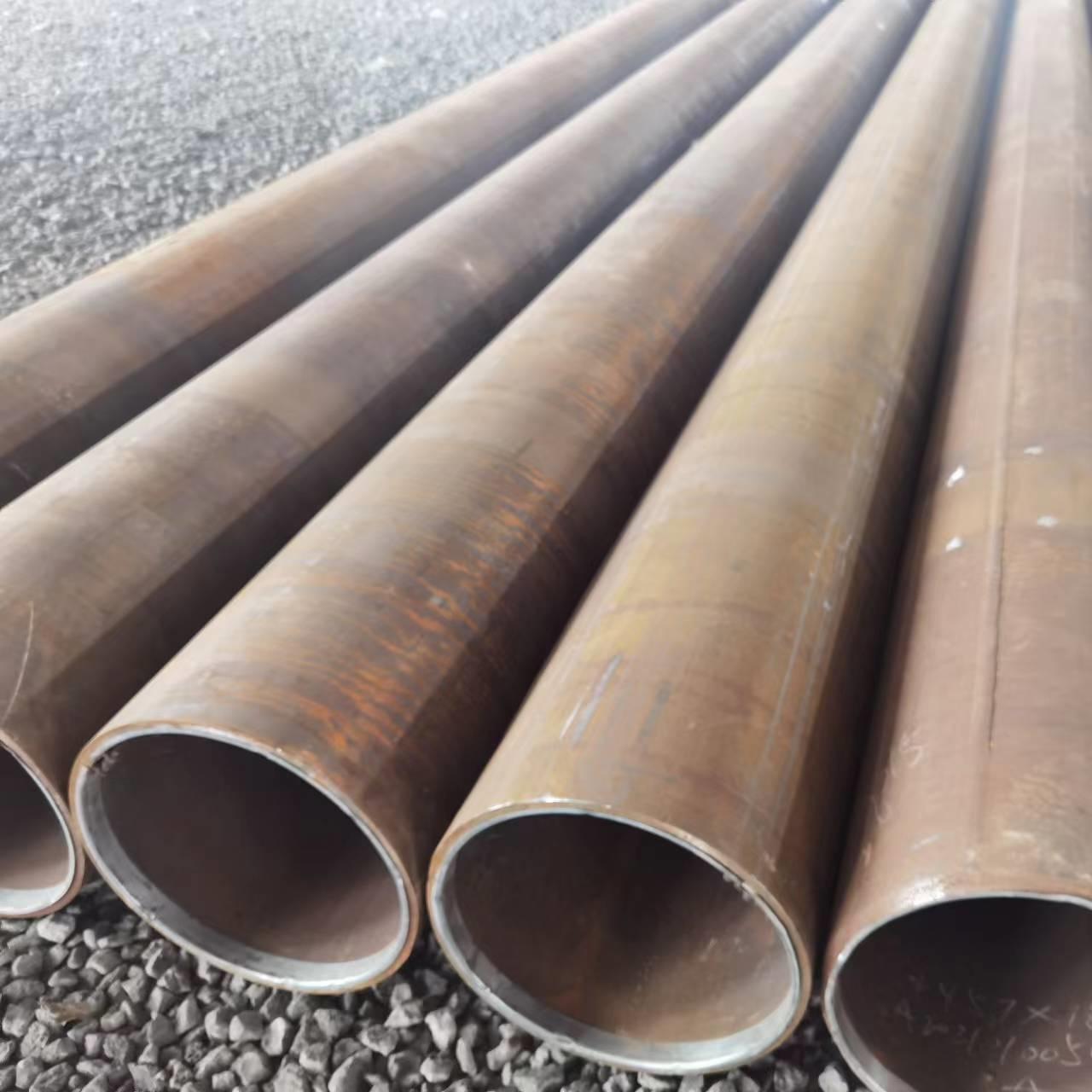
Additionally, HFW pipes have a smooth internal and external surface, reducing flow resistance and enhancing efficiency in fluid transportation Additionally, HFW pipes have a smooth internal and external surface, reducing flow resistance and enhancing efficiency in fluid transportation
high frequency welded pipe.
In the oil and gas industry, HFW pipes are extensively used for drilling, production, and transportation of hydrocarbons due to their robustness and resistance to corrosion. They also find application in construction, where they serve as structural components in buildings, bridges, and other infrastructure projects. Furthermore, HFW pipes are utilized in the automotive industry for exhaust systems, and in the manufacturing of scaffolding, furniture, and agricultural equipment.
The high-frequency welding technique not only ensures precision and efficiency but also reduces waste and production costs compared to traditional welding methods. It allows for the production of pipes in a wide range of sizes, from small diameter tubes to large diameter pipes, thus catering to diverse industrial needs.
In conclusion, high frequency welded pipes have become an indispensable part of modern industries due to their exceptional mechanical properties, versatility, and cost-effectiveness. As technology continues to evolve, we can expect further advancements in HFW pipe manufacturing, leading to even more efficient and durable solutions for various engineering challenges. The significance of high frequency welded pipes lies not just in their widespread use, but also in their contribution to the overall efficiency and safety of numerous industries.